Is the search for a reliable solution to equipment downtime a constant battle? The implementation of temporary replacement part solutions, particularly those offering comprehensive coverage, is not just a good practice; it's a strategic necessity for maintaining operational efficiency and mitigating financial losses.
The frustrating reality of equipment failure, a scenario all too familiar in various industries, often triggers a scramble for immediate solutions. The downtime, however brief, translates directly into lost productivity, delayed projects, and potential damage to a company's bottom line. The quest for a "Temporary replacement part 3 full" solution, as the search queries indicate, highlights the urgent need for readily available, effective alternatives. While the specific nature of "part 3" remains ambiguous without further context, the fundamental concept of a temporary fix resonates across sectors. From manufacturing plants to construction sites, the capacity to quickly swap out a failed component with a functional equivalent is paramount. This approach, even in the short term, preserves the integrity of operations and buys time for a permanent resolution.
The absence of readily available search results for "Temporary replacement part 3 full" emphasizes the importance of clear, accessible information and readily available resources. Businesses need a centralized repository, a directory if you will, of available parts and the suppliers who provide them. The current fragmentation of this information, coupled with the lack of standardized nomenclature, results in time-consuming searches and frequent delays. It's also critical to emphasize the importance of robust supply chains that anticipate potential failures. In this model, companies need to establish relationships with suppliers, maintain inventories of critical parts, and have contingency plans that address the unexpected. The goal is to transform what is currently a reactive process into a proactive one, minimizing the overall impact of unexpected equipment failures.
Read also:Bollywood Streaming Piracy Justwatch Bolly4u Insights
The pursuit of information, as indicated by the requests in online forums, goes beyond mere technical specifications. The reference to "early access" and "download links" implies a desire to engage with innovative technology. In the modern era, access to information and readily available resources often determines the success or failure of a business operation. With technological breakthroughs and the availability of tools and online platforms, businesses can improve the efficiency of their operations.
Consider the example of a fictional company, "Apex Manufacturing," which produces high-precision machinery. A critical component in one of its flagship machines, a complex hydraulic valve (we'll call it Part 3), fails unexpectedly. Without a replacement, the entire production line halts. The financial implications are severe: delayed orders, potential penalties for non-delivery, and lost revenue. This is where the benefits of temporary part solutions become immediately apparent. By swiftly installing a temporary replacement, Apex Manufacturing can restart production, minimize disruption, and ensure delivery of the goods. It's important to note that the temporary replacement is never meant to be a permanent fix. But it enables the company to continue working, maintaining their brand reputation while awaiting a more permanent solution. Without it, the situation could have been much worse.
Now, consider the crucial role of reliable suppliers. Apex Manufacturing, for example, needs to work closely with trusted suppliers, to have clear communication about the types of part that are frequently damaged and the best solutions to maintain production. In this case, Apex would identify reliable suppliers capable of providing quality temporary replacement parts. Regular communication with suppliers, maintenance of inventory levels, and pre-negotiated contracts all help prepare a business for the unexpected. The efficiency and speed of response are critical. The ability to locate and source a replacement part within hours, not days, directly influences the overall impact of an equipment failure.
It is critical to acknowledge the wider implications of equipment failures. They extend beyond the immediate costs of repair or replacement. The consequences can affect every part of the business, and a quick resolution saves money and strengthens brand trust. Customer satisfaction and employee morale will suffer. In the event of a prolonged shutdown, companies might have to deal with penalties imposed for delays. The resulting decline in customer loyalty further adds to financial losses. Temporary replacement part solutions, therefore, are essential for business resilience and continued success.
Let's delve into an illustrative case study to further highlight the critical role of this strategy. Consider a large construction firm, "BuildRight Inc.," which is undertaking a major infrastructure project. Suddenly, a crucial piece of heavy machinery malfunctions, jeopardizing the project's timeline and budget. In this situation, having access to temporary replacement parts for the damaged equipment would prevent the project from grinding to a halt. It would give the project managers time to order the right parts and prevent a slowdown that affects the timeline. By promptly replacing the faulty component, BuildRight Inc. could sustain progress, meet deadlines, and minimize any budget overruns. The temporary fix is more than a stopgap. It is a calculated approach to minimize the consequences of equipment failure and mitigate risk.
In conclusion, the emphasis on "Temporary replacement part 3 full" reflects the essential need for solutions when dealing with equipment breakdowns. Proactive measures and strategic preparedness are critical for maintaining business continuity and mitigating financial risks. Embracing temporary replacement part strategies and developing close relationships with reliable suppliers enable businesses to minimize equipment downtime and maintain their competitive edge. In today's fast-paced business landscape, quick and effective solutions are no longer a luxury; they are a fundamental requirement for sustainable success.
Read also:Frustrations Learn About Movie Tv Search Issues On Justwatch
Aspect | Details |
---|---|
Subject | Temporary replacement part solutions |
Industry Applications | Manufacturing, Construction, Logistics, Transportation, Energy |
Benefits | Minimizes downtime, reduces financial losses, maintains productivity, preserves project timelines, fosters customer satisfaction, enables efficient operations, improves business resilience, and boosts competitive advantage. |
Key Considerations | Rapid part identification and procurement, supply chain reliability, inventory management of critical parts, pre-negotiated agreements with suppliers, and proactive maintenance and inspection. |
Challenges | Availability of compatible temporary replacement parts, the cost associated with acquiring temporary solutions, the need for skilled personnel to install and maintain temporary parts, and proper assessment of the issue. |
Best Practices | Establish partnerships with trusted suppliers, implement a proactive maintenance program, maintain an inventory of critical spare parts, create a detailed equipment failure response plan, and use technology to improve efficiency and facilitate the search for parts. |
Emerging Trends | 3D printing of replacement parts, digital supply chains for faster procurement, and the use of predictive maintenance technologies to anticipate and prevent equipment failures. |
Resource | Example: Source of temporary parts |
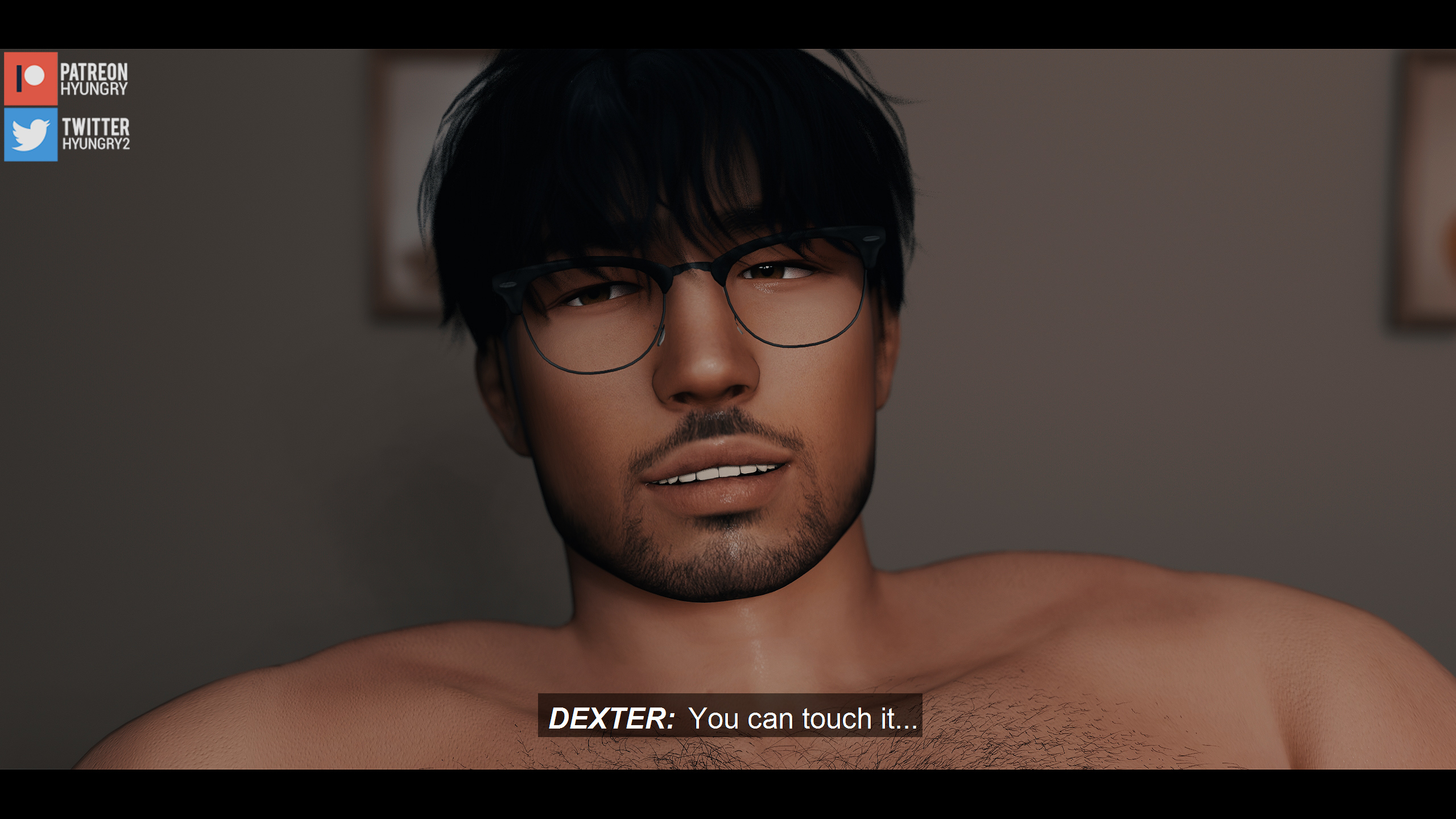
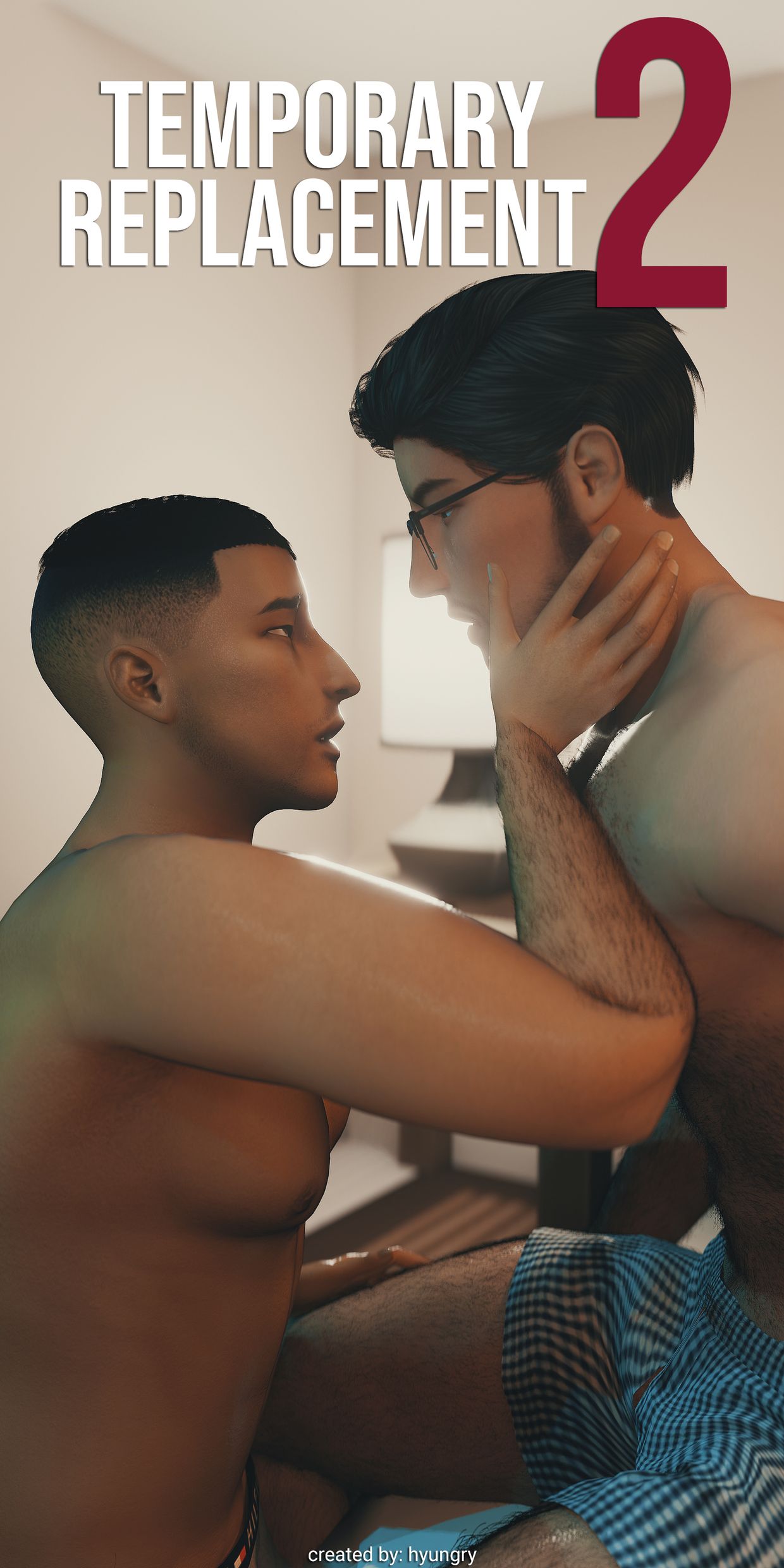
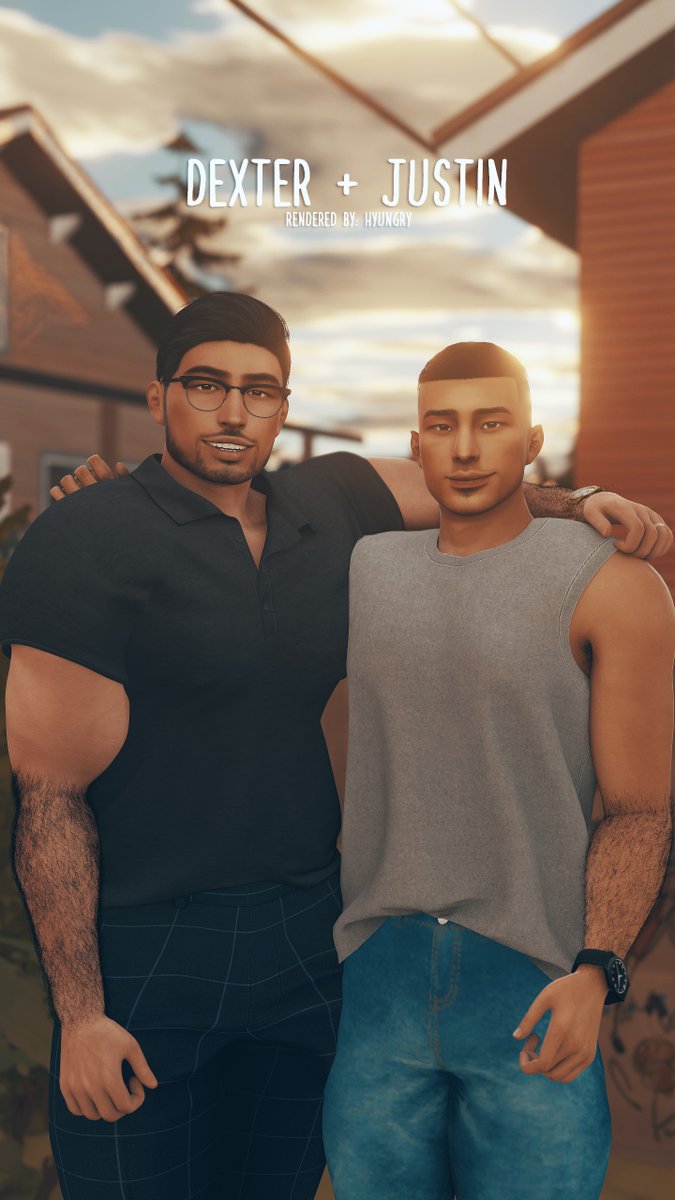